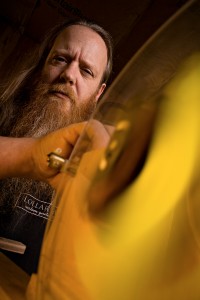
Get ready for “16 tons” of info about pickups in this month’s Spotlight feature on Jason Lollar. Based in the Seattle area for most of his life Jason started playing blues music around 1980 while also listening to lots of older funk, mowtown, jazz, rock and country. How he got into the pickup business was actually through building guitars. Players heard his hand crafted guitars and wanted the pickups for their own instruments. Seeing an opportunity Jason began winding his now famous Lollar Pickups along with writing a book (now out of print) about pickup building which many custom winders regard as their “bible”.
Jason Lollar’s pickups are no-nonsense nuts and bolts units that do their job and very well I might add. There are no fancy model names, no flashy ad campaign and no clichéd hyperbole. Just magnets, bobbins and lots of wire. So what sets Jason’s pickups apart from the literally countless pickup winders located in the dark corners of the globe? Winding and listening. Then winding and listening some more. And after that he winds and again listens. This process has been going on for the past 30 years. Jason is no “Johnny come lately” to the guitar pickup market. 30 years of winding and listening experience goes into each pickup. That’s a heck of a lot of soul to be dumping into a little guitar pickup but you can hear and feel it every time you pick up your guitar and start to play. Jason’s pickups make your guitar cooperate and deliver your music with toneful ease.
In this Spotlight segment Jason goes into detail about the build process, how he guides his customers to choose a pickup, adjusting pickup height for maximum tone and a whole lot more. This is one interview that you really need to pay attention while reading. There is a lot more info than you may think. Jason took time out of his very busy schedule to share his extensive knowledge with us. So without further adieu….
300guitars: Hi there Jason. First of all tell us what makes a great, rich sounding and dynamic pickup?
Jason Lollar: In my opinion it’s the overall vision, the combination of materials and the mechanical execution that makes the difference from a mediocre pickup to an excellent one. A firm understanding of the pickup design, why you are making it, i.e. the desired outcome and the way you are making it is very important. Matching the pickup or designing for the intended purpose is my first consideration. The erroneous comment I see is “its just wire and magnets how complicated could it be”? You can train someone to doggedly follow instructions but someone has to do the research, come up with the specs, the method and the materials used. You have to check out all the materials available and work or combine them to your best benefit. For instance- alnico magnets from different sources sound quite different, so you can’t assume all materials are the same. You also have to learn what you can manipulate to make your parts do what you want. It takes a lot of time and product running through your hands to get a grip on it, you have to be constantly testing and comparing the results or you won’t come up with any conclusions that have any basis in experience.
300guitars: With all the manufacturers and models available, how does a player go about picking a pickup? How do you guide your customers when they are unsure which model to pick?
Jason Lollar: There are many winders out there. I see one to two new ads for boutique pickups in every other new issue of Vintage Guitar magazine – that’s incredible! Find someone that can answer basic questions like “will this pickup fit in XYZ guitar?” There are so many details that can hang you up- if the pickup builder doesn’t know the basic answers then you’ve got a potential problem. They should be able to give you a reasonably good idea how a particular pickup will sound in your guitar, with your amp. There are lots of factors that will still be unknown, like your particular playing style but there should still be a fairly good idea how that particular pickup will perform.
I wouldn’t want to be trying to establish myself at this point in time- there is so much competition among the newcomers that you will definitely have to be on top of your game to get anywhere.
When I designed my line I kept the selection of each model limited- I looked around at some of the bigger guys- they often have a 20 or more different humbuckers! My business has a narrower focus; keeping the choices to a minimum has worked really well for us. I don’t claim to make something for everyone which guys like Seymour already have that type of business set up. They have the capability to service a wider range of people than I do. My customers have a narrower demographic but it turns out that what I do make is actually a good choice for a wide range of styles too, much wider than I envisioned.
The usual process when people choose one of my pickups is done a few different ways. Sometimes they played a guitar with my pickups installed, maybe a friend’s guitar or one for sale somewhere and they want something just like that so that’s easy to accommodate.
Sometimes a guitar’s sound is not ideal, so people are looking for something with more output or less output, more or less bass, punchier, smoother etc so they have a specific attribute they are looking for- that’s a little harder if you don’t have a good idea of what they already have. Sometimes I help select by the amp someone is playing- some pickups sound better in different amps but it’s really all subjective. One guy might like a dark tone with limited dynamics- some guys call that “greasy” and some call it “muddy” so it really depends on perspective and no one is right, everyone has a different result they are shooting for, so it can be difficult to hit the request on the head sometimes. Throw in the fact that each player can sound dramatically different than another using the same gear and that further complicates things. I try not to shoot in the dark, but sometimes you have to get a pickup in their guitar before you can figure out they want something different. Most tone guys are willing to experiment, it’s a journey. Its great- I’m willing too! You also have to be willing to refer them to another pickup builder, sometimes what they’re after, you don’t make. There is no shame there.
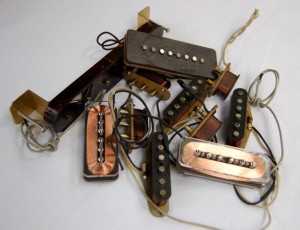
300guitars: Do you recommend that certain pickups match with certain types of wood and/or certain types of guitars? Or does a pickup sort of match with a type of music or style?
Jason Lollar: I don’t buy into winding a pickup for a certain type of wood anymore. Wood varies too much from piece to piece plus the design of the guitar and the way it’s built has a huge impact on the outcome. There are some general attributes but they vary too much to be able to predict specific results in an exact way. Of course there are historical examples that you can fall back on – Fender type bolt on neck guitars with rosewood fingerboards and alder bodies would have a pickup with a certain range of specs and light ash with maple necks another. You can select a pickup using historical examples or break the rules and in either instance you’ll find people that are happy with the results. I tend to rely more on- do you want a really clean and clear sound or something with a little more grit? Tight bass or smooth? Brighter overall or more midrange? I like to hear more about the overall results someone is looking for and I try to keep it simple. Don’t tell me it’s for blues- there is way too much variation in what a blues player sounds like. Think about the exact properties you would like to have- what’s important – tight bass or creamy tone? Take your amp into account- a tweed Champ that you dime all the time requires something different than a Fender Twin Reverb. Possibly not everyone is aware of it but you should be able to discern if something’s not you- “this sound is just not my personality”. For me it’s plainly obvious, when I am sitting around on my own I often don’t even plug into an amp but when I do I often run it hotter and more distorted than I would at a gig. I get to the gig and go- ewww, clean it up- roll that volume down a bit. I like a cleaner sound and I pound the crap out of the guitar at points and want to turn around and get clean at the drop of a hat. I like old Fender amps- give me something different and when the chips fall I probably won’t like it. There are a lot of people that have this awareness and are quite particular- that’s really what’s driving the whole boutique amp, guitar, pickup, pedal, cable, strings,…….you name it, if it affects sound, someone some where is working on making it better, making it different.
I have a pretty nice collection of vintage amps- lots of Fenders- tweeds through every era up to the Super Twin with 6- 6L6 tubes- the one that Nugent stacked on top of each other into a wall of amps- that’s actually an under rated amp! I have Vox, Marshall, Masco, Silvertones, Alamos and I have a few new amps- A Victoria Regal and a 65 London and I have direct access to many others- people that work with me and other guitar players in my area like to hang out and play through whatever we have to compare them to- whatever they brought over. I use all these vintage amps for designing pickups and I take them out and gig with them (on the rare occasions I go out and play a full night). I don’t leave them in the club overnight anymore like I did 20 years ago of course!
I have found (and not everyone agrees with this) that if your not getting a good tone out of an amp with the specific guitar and pickup that is often just a matter of plugging into a different amp- serious- just a different amp can make all the difference in the world.
Of course not everyone has that option, so we often wind up selecting a pickup for them that will work better with their current amp. You also have to remember to use the tone controls on the amp- we tend to fall into a pattern where we set the controls and don’t think about it- another guy will come in and grab the same guitar and amp- set the controls a little different and get a dramatically different sound. Top that off with not every 1958 Fender Deluxe sounds like another 1958 Fender Deluxe, couple that with the room you have the amp in. We’ve all had this happen if you played a lot of places- one night you’re getting killer sound and the next you’re in a different room and can’t get it dialed in at all- maybe the room has brick walls on three sides and glass all down the fourth. Also most clubs don’t put the band in the ideal spot- the bandstand is usually an afterthought. The best players are the ones that get a consistent sound night after night- that takes effort; it doesn’t just happen to you.
So getting back to the original question- am I going to design a pickup differently for a 4 pound alder body verses a 4 pound 9 ounce? I don’t think so. When it gets to the point of splitting hairs and getting consistent results across the board- it doesn’t work that way in real life.
I am just pointing out what you are up against but pairing the right pickup with the right player, it’s amazing how often I can get it right if you consider all the other factors involved that can throw you off. These are all reasons I try to keep the choices simple. I try to make each model of a specific design like say one particular model Strat pickup for instance, sound noticeably different than the next model Strat pickup I design, no little half steps, that way people will be able to hear a discernable difference and will be able to make a choice in a more general manner.
300guitars: When you manufacture a pickup do you use age old methods or blend in some new technology?
Jason Lollar: I use a combination of hand guided winders and old commercial winding machines depending on what results I am after. My commercial machines are completely mechanical, meaning they have no computer and they are based on 19th century yarn spooling machines. They are old school and they are set up to have variations from layer to layer of winds due to the geometry of the wire guides and the vibration I build in. I make every part of the machine that holds the bobbin and guides the wire, so I have complete control over how I build inconstancy with consistency! It would be difficult to explain with words alone but you can set up an old machine like this to simulate someone winding randomly. The first machine I made back in the late 70’s was made to try to automatically traverse, I have never been afraid to experiment with this part of the procedure, back then no one was claiming hand winding was superior to an auto traverse machine like the general view is now, so I didn’t know any better, which freed me up to experiment with auto traversing and with various methods of tensioning the wire.
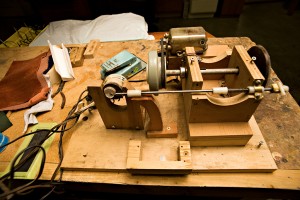
Today’s dogma is that hand wound is always superior to machine wound- well I would bet most of the guys claiming that do not have a commercial winder to compare the difference- really! I have compared and I can’t say one is better than the other, they do have some differences but it has nothing to do with quality of sound. You can make a crappy hand wound pickup very easily.
All in all most of what I do is based in old technology- electromagnetic physics- the same kind of science that lead to the industrial revolution- its that old! I do use various testing methods they didn’t have back then like spectro analysis where I send off a piece of an old part and they vaporize it, running it through a computer that tells me the exact percentages of every element contained- very useful for finding out the exact materials used in vintage pickups but not necessarily significant.
Also I took about a year worth of college drafting courses back in the late 80’s or early 90’s when I was a starving musician. We learned to do line drawings with pencil and pen and we learned blueprinting and orthographic projection. Back then they were just starting to show some rudimentary AutoCAD methods which it turns out I use almost daily now. Being able to draw up parts in cad really put me into a different position than I was 30 years ago!
I started using a computer drafting program (AutoCAD) probably around 1995 to help me cut parts by hand more accurately with more repeatability. I bought a laser cutter about 4 or 5 years ago. Before that I made all my parts by hand from scratch- drill press, table saw, router, tin snips and coping saw. I cut out probably over 1000 tele base plates by hand with tin snips. I made thousands of P-90 bobbins with a table saw, router and drill press. Remember back then- even 10 years ago there was no place to buy parts like strat pickup flatwork. Its only been in the last 4 or 5 years where you can get a lot of these items pre-made and they are a lot easier to find, for instance you can buy just about anything you need at Stewart Macdonald’s. My book on pickup winding had a huge impact on the accessibility of parts for people, it created a market that wasn’t being serviced before and it alerted a lot more people to the possibility of making their own pickups.
The laser I bought will cut plastic, wood and it will scribe mother of pearl and certain types of metal but it won’t cut metal all the way through. I send out any major metal cutting to places that have water jet cutters for smaller batch items, some stuff I still cut by hand in shop but water cutters and lasers really opened up what I can do. The laser will cut things you never could by hand because a laser doesn’t apply any pressure to the part being cut- this means you can cut intricate parts that would have just shattered with a router. These kinds of tools allow you to make smaller quantities of parts without having to invest in a punch or stamp. A laser or water cutter can be changed quite easily to make corrections where a stamp can not, it makes my life so much easier and all the parts come out perfectly every time!
Thinking back how many thousands of parts I cut by hand its incredible. If you saw how many CAD drawing I have of old and new pickups you would probably be amazed. I often draw several parts daily going back more than ten years. I keep specs on anything unusual that passes through my shop for repair. So really the biggest thing that has changed for me is getting that laser cutter. I could cut all that stuff by hand before but this is a whole different thing. So once again getting back to the original question, basically to make a Strat pickup- I go to that because it’s fairly simple to envision- first you have to cut out the top and bottom plates or flanges which is usually called “flatwork”. I use the laser cutter which is about the size of a large copy machine but it’s basically a printer, or more accurately a plotter, but instead of ink it shoots a laser which vaporizes the material in a very thin line where you want it to cut. It will also engrave to varying depths rather than cut all the way through. Once your parts are cut, you punch in a couple eyelets for soldering the coil wire to the lead wire and then you are ready to install the magnets. Of course first you have to bevel the magnets- if it’s a design requiring it, like a stagger pole strat pickup. I chuck up each magnet into a hand drill and run it over a belt sander to put a slight bevel on each edge. I use a vintage bevel like you would see on a 50’s strat, so it’s actually very slight- almost unnoticeable, unlike what Fender does today. I have to handle each magnet individually so it takes some time, if you have to make 30 pickups that’s 180 magnets. Sometimes I bevel several hundred- one after another at one sitting. After that I pound each magnet into the bottom plate one at a time. The trick is to pound it in perfectly vertical every time or you wind up spending a lot of time trying to straighten them out. Once you have to tweak the magnets to correct the placement, the pickup never comes out quite right. I still do them one at a time with a rubber mallet but am just about to switch over to a foot powered press that will put in all 6 magnets at once and come out perfectly straight.
After the magnets are all in straight, I pound the top plate on and set its position with a spacer block so that the plates are an exact distance apart from each other and the coil has room to be wound on. Next insulate the magnets so the coil wire will not short out. Even though the coil wire is insulated it still can short out to the magnets resulting in inconsistent tone and performance. I tape over the magnets with a thin tape which I think is superior to the dipping in lacquer method Fender used back in the day which resulted in a high percentage of shorted coils- not dead and unfuctioning but very inconsistent!
After that I wind the coil using whatever method I determine works for that pickup and I tape over the outside of the coil. Again the biggest failure for Fender pickups is the coils are left unprotected, you can kill the pickup by putting a pickup cover on it! After that I solder on the lead wires and tap the height adjustment screw holes for 6-32 screws. Most strat type pickups are not tapped- they give you self tapping height adjustment screws and hope you install them correctly! At this point you can wax pot or not. I take into account the pickup and guitar design and pot each pickup to a specific amount- I time it; some get more and some less. It results in a very consistent amount of microphonics from pickup to pickup within each type of design.
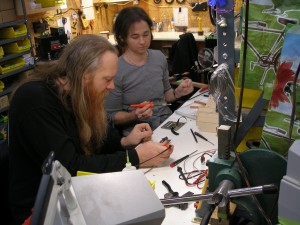
This is a stripped down version of what I actually do. There are a lot of tests points during the whole procedure including viewing each pickup with a magnetic field viewer, testing the inductance and comparing it to data collected for that design over a number of years. We also use a gauss meter and an ohm meter- most often more than once, there are approximately 10 to 15 individual test points for every pickup including electronic, mechanical and visual tests for every pickup. It boils down to a lot of handwork regardless of whether you use a commercial or handwinder. The winding portion is the smallest amount of time spent. This brings me to the often repeated “crappy pickups made thousands at a time on a machine” scenario that is often coupled with “hand wound pickups are superior to machine wound” statements. Yes there are machines set up to wind several coils automatically at the same time so you can save some time on the winding end of it- sort of- but you would spend so much time getting it set up to run one cycle I am not sure if it would actually be faster or not. You still have to load tension and tie off each bobbin mounted to the machine before you start it up. I guess if all you did was run that machine all day and did nothing else you could save some time but it still boils down to winding the coil takes the least amount of time for the whole process. You could have a computer programmed auto traverse machine that copied every move a hand guided winder operator made! You would basically have a robot that copied every move Leo Fender made if Leo was still around. Really the poor quality comes from unskilled labor or trying to work too fast and letting what should be rejected go through and or by cheap or incorrect materials possibly even made with flaws combined with unskilled or uncaring labor.
Another factor in these quick to make, cheap pickups, I’m talking about $30 strat pickups etc – does anybody even listened to them or if they do- with any kind of critical trial? Combine no critical R+D with unskilled improperly trained labor, poor quality parts, with inconsistent supplies and a price driven manufacturing philosophy and an unwillingness to ruthlessly reject any defects or have a low threshold of what is passable, taking for granted that the manufacturer knows what and when to test to find defects because they often don’t- All that leads up to the end result of crappy pickups. Although I will say that crappy pickups that fall apart immediately or short out immediately are not as common as they use to be but there are a lot of pickups that are only passable. I have seen brand new pickups where you turned them upside down and all the screw pole pieces fell out! I have seen several loops of coil wire wound completely off the bobbin and then shoved under the pickup cover- stupid stuff!
I don’t think its impossible to mass produce good products but it is extremely difficult, everyone involved in the process has to be at the same level, no one can pass off shoddy work to the next guy and still have the end result as good as it can be. Those cheap imported pickups are really not that good of a deal when you realize the importer only pays around $2 – $5 dollars apiece for them and then turns around and charge you $50 or more. That’s a lot more profit built in than the most experienced manufacturers run at!
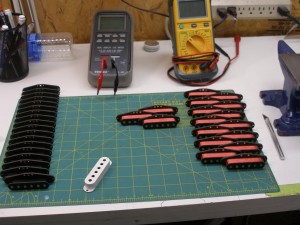
300guitars: How does the tension of the wire while winding affect the performance of a finished pickup? Is tension adjustable?
Jason Lollar: Tension is adjustable and there are various methods of doing it, some winders that guide by hand also tension by hand- one method is to use a piece of felt between your fingertips and squeeze it while you guide the wire back and forth- that’s the most basic hand tensioning. I have always used a tensioner that I run with a fixed amount of tension, basically it’s a piece of felt with a clamp, I run the wire through that and tighten the clamp down to the amount of tension I want- that takes a bit of practice to be able to feel how much tension to apply, just like hand tensioning. It’s not a passive procedure that you only have to check once- it will need to be reset every other pickup or two depending on a lot of things. Without getting too deep into it, there is a wax they use while spooling the wire at the factory. If the amount of wax varies it will build up on the felt faster or slower and its something you have to continuously monitor. There are also mechanical devices that will actually measure how many grams of tension are on the wire and are made to keep the wire under a steady amount of tension but most of those are designed for use while making cylindrical shaped coils rather than the more commonly used oblong shape that guitar pickups are made with, so they tend to break the wire and give you uneven pressure. I know there are ways to use a dynamic tensioning device but it’s not something I have explored beyond some initial trials. Poorly tensioned coils can be overly microphonic to the point of being unusable. A loose coil can be much larger than a tight coil so it can sound fatter but it can also affect inductance in unexpected ways- inductance has some effect on frequency response, dynamics and perceived output but its not a be all end all factor. If you wind too tight you’ll loose a lot of the funk that a coil with some level of microphonics has. You can also wind so tight the coil wire stretches and gets smaller- this will definitely skew the results you expect and you can actually get so much tension accumulating that you can snap magnets in half or warp or break bobbins.
It’s something you have to constantly monitor even if you don’t have a scale and are just doing it by feel. If you don’t have consistent tension your pickups will vary in tone quite a bit even if you are winding them to the same specs (other than tension specs of course)
Tension is just another example of something that takes experience to know what to expect and find out what works for you from a manufacturing standpoint. Once you come up with a line of pickups that’s when these small things start to become more important so you make a consistent product. The trick is to be consistent and yet not built out the unique tone in that pickup design.
300guitars: There are some hum-canceling stacked type pickups that sound pretty darn good but do not quite sound and respond like true single coil units. Why are single coil pickups so noisy and why is it that a stacked unit does not exactly replicate the sound and response of true single coil pickups?
Jason Lollar: I have heard a few stacked pickups that were pretty close but even with those you’ll hear some difference if you directly compare them to a single coil. The best stacked pickups I have heard are possibly the Kinsman’s. Compare these to a single coil and you’ll at the least hear a difference in the harmonic content and how the harmonics will change over time while you hold a note. The dynamics and attack are quite different in a stacked pickup. There are ways to work around it but there are some fundamental differences. Let me say that this isn’t an area I specialize in and I haven’t made a lot of them so I don’t know a lot about them.
One way to try to work around it is like what Gibson did with the P-100, rather than connecting the two coils in series which thickens the tone and boosts output and smears the attack they wound each coil very hot and connected the two in parallel which brightens the result, makes the bass tighter and has sort of a pseudo single coil tone. I don’t think it’s very successful at recreating a P-90 if that’s what they were after but it’s an example of manipulating the design.
As far as noise there are two we are concerned with, 60 cycle and 120 cycle. 60 cycle is what humbucking pickups reduce or eliminate and 120 cycle is what shielding helps eliminate and is why your strings are grounded. Not every player knows the strings are grounded to minimize some of the hum! It’s normal for the guitar to get quieter when you put your hands on the strings. I figure if you are up there on stage and you are not playing you’ll at least keep one hand on the strings if not roll your volume control on the guitar all the way down. I do that all the time- I turn the volume all the way down on the guitar if I am not playing. I don’t stand there with the amp cranked and my hands down at my sides.
You need to make sure you don’t have your amp plugged into the same circuit as a dimmer switch or ceiling fan is wired to; those are the biggest source of uncontrollable noise. Most of the time I have found if the noise is actually unbearable- you can hear it over the volume of the music then the PA is going to have that kind of noise too. It’s not just the guitar, you’ve got a problem and eliminating the guitar from the equation isn’t going to help. Of course I stand in the sweet spot and I always have one RWRP pickup just in case for a bail out if I am running single coils. That way if I do wind up in a bad situation at least I can hit that humcancelling pickup combination. Worst places I have played aside from running off a generator out in the woods at biker parties has been these small cruise boats they run on the Puget sound- not those big Bahaman boats, were talking funky old scows with hellacious power supplies- one big racket!
300guitars: Is there any other way to eliminate the noise but retain the sound and dynamics of a true single coil unit? What about a dummy coil for canceling noise?
Jason Lollar: Like I said I haven’t found it to be a big problem and I have played a lot- I have done some split bucker work- sort of like a P-bass but inline not staggered and there are – well I could write a whole article on that and the problems with those that occur.
I haven’t tried the backplate for Strats that John Suhr is marketing or manufacturing- I talked to John for some time about it and how it works but I have yet to try it. I have heard encouraging things about it from those that have. I have tried dummy coils myself but have not come up with anything that hasn’t dramatically changed the tone or reduced volume but like I said I haven’t had it be a big problem and it hasn’t been a big concern to my customers so I haven’t spent much time on it.
300guitars: What are the optimal measurements for setting the height for your pickup models and how does the pickup height affect the overall sound of the guitar?
Jason Lollar: You’ll get more of the tone of the pickup if you raise it closer to the strings and more of a neutral tone or tone of the guitar itself- in a way- if you have it lower. The actual height is going to vary from guitar to guitar and player to player. You will notice there is a sweet spot a pickup likes to be in but even that is all debatable, what one guy likes another won’t but because I often use magnets that are not fully charged many of my pickups are more sensitive about their placement. Everyone uses a different gauge string- they hit harder or softer from each other and the action will be set differently so you can’t just say go 1/16″ away from the string because a guy with light gauge strings will be deflecting them so much when they dampen that they will hit the pole pieces. One thing you hear all the time that I don’t agree with is you are suppose to set the pickup height while depressing the string at the last fret- well how often do you play that high? How often do you play above the 15th fret? Obviously you might once in a while and you don’t want the pickup to get in the way and hit the strings when you do play up there but depending on what your action is like- well it may be moot but perhaps not, depending on the action but I set the pickup where I am likely to play- somewhere between the 5th and 10th fret as an average. What most people get wrong is Fender pickups have a lot more string pull than Gibson style. On a fender strat with alnico 5 you’ll have between 900 and 1200 gauss- it’s just a measurement of magnet strength- on a Gibson it’s going to be about 200 which is a huge difference, so Gibson pickups can go extremely close to the strings. Also you can set your bridge pickup higher to the strings than the neck. The neck pickup is in an area of the string where it has a lot of leverage to deflect it and at the bridge hardly anything will deflect the string- there is no leverage. You’ll hear a weird way out of tune sound if you get the pickup too close- a warbling almost vibrato like tone. All in all it’s really about what sounds good to you. About a month or two ago I put up several videos on pickup adjustment and installation on YouTube. There is one on adjusting Strat pickups, you should check it out. I also have installing Strat pickups and installing mini buckers- very detailed and in depth with a lot of side notes dealing with all sorts of related topic within each video- anecdotal information I have spent years learning. Click here for Lollar Guitars YouTube channel.
300guitars: Potting is very important for preserving a pickup’s windings over time and keeping it stable from excessive feedback at high volumes. Can a pickup be over-potted and lose some of the “vibey” quality?
Jason Lollar: Most of us can easily hear the vibe that a microphonic or slightly microphonic pickup has, its like reverb almost or harmonizing a scale- a little extra air in the sound. If you over pot then you’ll kill it for sure. Every pickup I make is potted to some extent, every design has a different level of potting and I time it closely. I have a really consistent result the way I do it. I use to not pot anything- everything I made was unpotted. I mistakenly attributed potting to sloppy manufacturing and I printed it in my book. Now that same line I said has become part of the dogma going around but after making thousands of pickups I realized if I drop this pickup the whole coil is going to expand like a balloon and it can even come off the bobbin. This happens with vintage pickups all the time, un-potted coils can shift or slip and become un-useable, they can short out or even come completely apart!
On Fender coils, part of what holds them together is the potting. The trick is to get a certain level of microphonics you can hear so the pickup is sweet and yet have enough to prevent the pickup from becoming more microphonic over time or at worse falling apart!
It takes a lot of attention to do it right. If you looked at my Fender style pickups most people would not be able to tell they are potted- I am meticulous about wiping off the wax; there is no reason for sloppy work under any circumstance except for ineptitude or having to do something in a hurry. Not that I am slow, I don’t doddle. Once in a while I will have to pot something more for a guy using a lot of gain. Most people haven’t caught on to this yet (I need to make a video on it) but the way I pot my pickups you can actually adjust the amount of microphonics you get by clipping down the springs to get a looser mounting on the pickup so that you can get more microphonics. You can even pop the metal plate off the bottom of the Tele bridge pickup to break the wax seal. A vibrating reflector plate on the bottom on a Tele bridge pickup will definitely increase the amount of microphonics to the point it will be difficult to control which is a lot of the sound Roy Buchanan use to get. On the other hand you can get less microphonics by tightening the mounting screws to put more pressure on the springs holding the pickup in or stuff a little bit of foam under the pickup to keep it mounted more solid. If you wanted to eliminate even more of the microphonics you could replace the springs with surgical tubing. Vintage fenders used Surgical tubing but my pickups are designed with springs in mind.
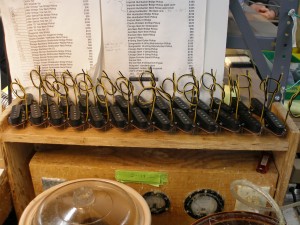
300guitars: What are some of your favorite pickup designs that you produce?
Jason Lollar: I have been playing humbuckers since I was 11 years old or so and I am 48 now so they have been part of my life, my main go to guitar is a 335 but I also love single coils, P-90s are a great single coil that even a guy that only plays ‘buckers could probably get along with once they got use to that much more dramatic dynamics- its almost like being naked all of a sudden- every aspect of your playing that is not dead on is revealed with single coils!
Jazzmasters- I love my 59 Jazzmaster, mini buckers are highly under rated, you should hear mine. Firebirds are almost single coil-ish, I like those a lot. I just got a pickup made a couple nights ago, it’s a copy of a Supro/ Valco/ National just like on Ry’s first “coodercaster” buts its made to retrofit, the bridge is not incorporated into the pickup like the original. I got the first prototype made a few nights ago- I am really excited about it. To see the complete metal assembly, drawn up, cut, buffed, plates and assembled, making every part from scratch is a blast (I’ve actually make a lot of one of a kind pickups). The tone was way more than I had expected- very powerful pickup with an extremely clear overall voice. There is a little bit of partial out of phaseness that gives it a little bit of cluck that makes it have a unique character no other pickup has.

300guitars: What is on the horizon for you and your company? Are you going to come up with some totally new designs?
Jason Lollar: I went from one guy struggling and busting my butt everyday to busting my butt everyday with 12 people. I am hoping to keep everyone busy in this economy. I have fought growth from day one so I could keep my quality where I wanted it but still wound up growing. I have a lot of new things up my sleeve, products that people have consistently requested me to do like a pickguard mounted humbuckers for jazz guitars, and I am going to make a copy of the McCarty pickguard, pickup combo for jazz rigs. There are some cool things coming up at least half driven from listening to customer’s requests and also just my own interests in what would be cool. I have a huge backlog of stuff I make that I don’t advertise so I am going to release them here and there and make them production items- something I keep in stock and make a batch at a time which lowers the cost for me to make it- get it off my custom list and put it onto my standard production catalog. I don’t necessarily care if I sell a whole bunch of an item but I do like having some things that are fun to make and are an impressive bit of work that most people will recognize as being something special and different. I rarely make anything “new” it’s usually old designs revisited or have some unusual twist not done before
300guitars: Thank you very much Jason for taking the time to answer these questions about pickups. I am a big fan of your products and each model I got from you sounds fantastic!
Jason Lollar: There are so many people I have met in this industry that are straight up cats that have a lot of talent and motivation. I appreciate all the other guys doing similar things to what I do- you’re one of them. I get a lot of use out of that Blonde Bassman cab you made for my 64 tuxedo head a few years back, good job all around.
Whatever each of us does to service the industry like we do builds the demand for high quality manufactured product- I mean handmade! You know? We are all in it together.
Visit Jason Lollar Pickups here for more information and ordering.
Check out the review of the Lollar Imperial Humbuckers here.
Lollar Guitars YouTube Channel here.