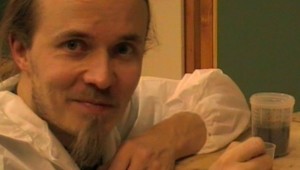
Juha Ruokangas has just completed his latest guitar model the Unicorn. Using his tonewood recipe Juha has created a handcrafted instrument that is balanced and built for the discerning guitarist. This is a labor of love that was documented every step of the way for the entire world to see on YouTube. In this follow up interview Juha talks about the Unicorn, the filming process and some challenges he faced throughout the building process.
300guitars: Hi there Juha. Congratulations on the success of your Project Unicorn! That was quite an undertaking. How do you feel now that it is complete?
Juha Ruokangas: Thanks Billy, you’re right it was quite a project, didn’t realize beforehand the vast amount of work this would be. Now that it’s complete I feel happy and relieved – sort of confusing mix of emotions. I am so fortunate of having Emma by my side, without her effort this definitely wouldn’t have been possible.
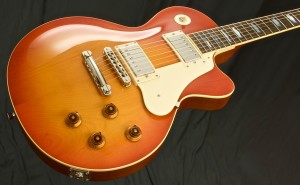
300guitars: So going back to the beginning, what were some of the criteria of designing the Unicorn?
Juha Ruokangas: I have designed my Duke model a long time ago, and at that point I wanted to explore the Les Paul style guitar concept, but to come up with a more modern guitar aesthetically and ergonomically speaking. Now, more than 10 years later, I’ve come back to “my first love in electric guitars”, the Les Paul. This time I wanted to challenge myself in creating something with strong retro feel and identifiable roots, and bring to the table my 15 years professional experience with the specific tonewoods I’ve been using for ages, but which are very unusual in the world of electric guitars. Also I wanted to focus in improving certain weaknesses (literally so) of the Les Paul guitar.
300guitars: Do you feel that you hit the mark and the end result Unicorn turned out like you wanted it to?
Juha Ruokangas: Absolutely. I know for a fact that Spanish Cedar is the most amazing tonewood in the world to challenge the good old lightweight Honduran Mahogany, and the tonal combination with the ThermoTreated Arctic Birch works SO beautifully – still gives me goosebumps every now and then when I play Spanish Cedar guitars… The constructional improvements of the Unicorn will certainly pay off in the long run – I give 20 year warranty to each and every one guitar we build, and that brings us certain responsibility concerning the quality of the instruments. Naturally its way more work to do the neck like I do it (as compared to the traditional way), but to me the end result definitely is worth the extra effort. Aesthetically speaking… I hope I don’t sound all full of myself here 🙂 … I love the way the Unicorn looks. It has the curvaceous shapes I like so much in Les Paul, and the slight changes in the body symmetry and the jazzier looking cutaway just do it for me. I’m also very happy with the headstock shape, I feel I managed to capture the “old look” in it, and at the same time you can tell its original – and it fits to the style of my previous designs with the 3D carve.
300guitars: What was the most challenging part of building the Unicorn?
Juha Ruokangas: There were several challenging phases. I kept drawing the bodyshape for weeks, then making templates, redrawing, new templates and so on… However, the most challenging part of the design must have been the neck construction – how to maintain the 17 degree headstock angle AND improve the stability, bend strength and durability AND at the same time install our 2-way truss rod in the neck. I didn’t count the hours of drawing and making the jigs to install the truss rod the way I did, but at some point it really felt like a lifetime! The whole puzzle of making the neck out of 3 slices of wood, joining the headstock to the neck, fitting in the maple splines under the headstock veneer and fretboard, routing and drilling in the truss rod cavity with maximum amount of wood untouched – felt like miniature bridge engineering! And afterwards, when I saw the edited video (6 minutes long or so) I remember thinking – oh wow, that looks easy – some pretty efficient, fast and precise working there! Wasn’t like that at all in real life…
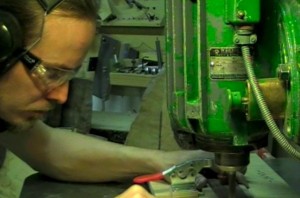
300guitars: Did you find it to be distracting to have a camera capture your every move working in the shop?
Juha Ruokangas: At first it felt really awkward to work like that. The guys at the shop kept teasing me about it – “the boss doesn’t work anymore if the camera’s not rolling”… Well, apparently you get used to everything – after a while I didn’t think about it anymore, felt like a natural thing. Another reason for the awkwardness was, that usually such design processes are done behind closed curtains, and I too did have my doubts at first about revealing everything – you know, business secrets and all that – but soon enough I realized that when you give, you get back so much more. All the feedback during the process, the enthusiasm from the watchers – I felt like connecting to the players in a way that had never happened before.
300guitars: Did the camera and documentation slow down the build process of the Unicorn?
Juha Ruokangas: Oh yes it did, big time. We’re a tiny company and the resources for executing this project were very limited. It was just Emma and me, and the schedules needed to be synchronized close enough so the actual building process and editing new episodes would go hand in hand. Sometimes this caused quite a bit of challenge, we noticed that the timeline of the building didn’t always go in a logical way – I was jumping back and forth with various parts of the design, and it was difficult to tie all that up to a 5-6 minute video episode that made sense. So.. Emma and me ended up sitting down every week or two to write down an actual script to keep things better organized!
300guitars: It looks like a lot of people watched your video diary clips. Did you expect to have so many viewers interested in the project Unicorn?
Juha Ruokangas: I’ve been completely blown away by the success of the videos. The first episodes have already almost 8000 viewers (and more day by day!), and for such “narrow margin interest” stuff that’s pretty amazing! Emma has done tremendous job with them, and I’m very happy that the viewers seem to recognize and appreciate her effort as well. One cool aspect of the project is, that when me and Emma go to the guitar shows, most of the visitors have watched the videos and they come to talk about it and they know already so much about the Unicorn guitar. It’s whole new territory for us, and we’ll definitely keep doing video projects in the future also.
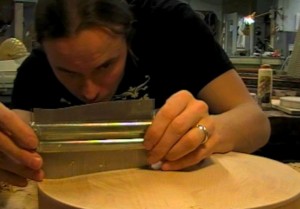
300guitars: When will you start taking orders for the Unicorn and when will production begin?
Juha Ruokangas: We’ve been taking orders for some time now. So far everything has worked kind of backwards – we haven’t marketed anything (except for the videos) – yet we have loads of confirmed orders already. We build about 100-120 guitars a year (total of all models together), and our capacity for 2009 concerning the Unicorn is 25-30 guitars max. By now we’re selling the Unicorns for 2010. As we speak, we are starting the production – which in our scale means, that we’re starting to build the first batch of 5-10 guitars.
300guitars: What is next for Ruokangas Guitars?
Juha Ruokangas: I feel very happy to be right here right now! 🙂 We still have a lot of work to get the Unicorn started out. Simultaneously we’ve been rebuilding our website for many months, and I hope the completely new site will be up and running in a month or two. The Unicorn will be naturally part of the new website as well, and we’re developing our Virtual Workshop guitar builder to another level as well – wait and see! Our most important future plan however is not to rush anywhere, and not to grow bigger. Things are very well in balance as they are now.
300guitars: Thank you very much for taking the time out of your busy production schedule for this interview and congratulations again on the success of your new Unicorn! It looks and sounds awesome!!!
Juha Ruokangas: Thank you so much Billy, it’s been really a pleasure to do this project and I truly appreciate that you wanted to include us on your awesome site. Keep up the great work!
For more details about the Unicorn and all Ruokangas guitars: www.ruokangas.com